Making Robots More Productive - What is Fenceless Safety?
Over the past 30 years, there have been very minimal robot-related workplace accidents and deaths according to OSHA incident reports. That is a relatively low compared to overall fatalities and accidents recorded by the U.S. Bureau of Labor Statistics during this time period. Of course, an ideal work environment wouldn’t have any accidents. While we haven’t quite reached this goal, automation seems to be a step in the right direction.
There are very specific safety parameters to follow when integrating robotic automation system. Items such as fencing, arc glare shield, and dividers are legal requirements to increase worker safety.


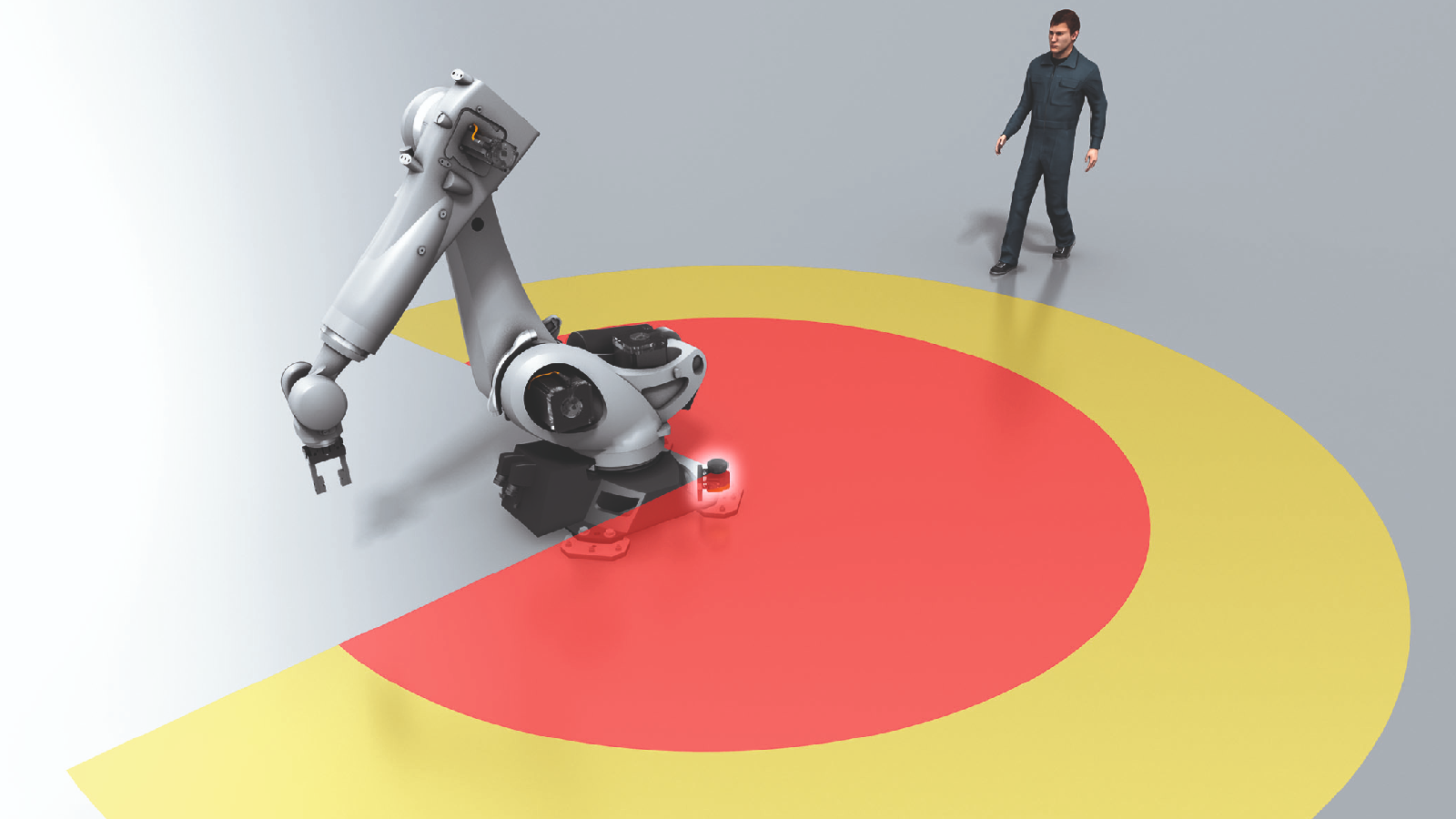
Could your robotic safety solution be slowing you down? Are hard guards, mechanical fences, and perimeter guarding devices eating up floor space that could be used for more productive processes?
An emerging concept – fenceless machine safety – is introducing machine builders and end users to a new method of safeguarding personnel and process integrity, while providing better access to machinery, facilitating quicker changeovers, and saving valuable floor space.
What is Fenceless Safety?
Fenceless safety relies on a non-contact, opto-electronic presence-sensing device called a safety laser scanner. The laser scanner monitors hazardous areas of machines by scanning its surroundings in two dimensions using an infrared laser beam. It works on the time-of-flight principle, which measures the time it takes for a light pulse to travel between the scanner and an object in order to calculate the object’s distance.
As soon as the safety laser scanner detects an object or person in the protective field, safe machine shutdown is initiated. Warning fields can be used to detect an intrusion before the actual hazardous area, signaling an audible or visual alert, or machine slowdown.
4 Benefits of Fenceless Machine Safety
1. Fenceless Safety Increases Productivity
Hard guards or mechanical fences limit access to your machines, and make changeovers more complicated and time-consuming. They occupy valuable real estate on the shop floor that could be used for value-added processes. Safety mats, light curtains, and other perimeter guarding also consume extra space for installation and the required safe stopping distances. On the other hand, fenceless safety is a non-contact solution, saving floor space and improving access to machines for quicker changeover.
2. Fenceless Safety is Custom-Fit to Your Application
With fenceless safety, the laser scanner is used to make the safety solution fit the application, rather than force the application to conform to the safety system. The scanner’s monitoring field conforms to the unique shape of the machinery and hazardous areas, without impeding worker accessibility and process productivity.
3. Fenceless Safety is an Out-Of-the-Box Solution
Unlike their hard-and-fast counterparts, fenceless safety is an out-of-box solution. With safety laser scanners, you simply disconnect power to the scanner, move it to the new location, and reconfigure the new safety zones using the built-in software. It’s that simple.
4. Fenceless Safety is Affordable
The machine tool industry has long been enticed by the idea of fenceless safety and its flexibility and space-saving benefits. The technology costs, however, simply outweighed the advantages. Now the prices of safety laser scanners have dropped significantly to where fenceless safety is a viable, cost-effective option.
Conclusion
Machine builders and end users should consult with a safety solutions provider to determine the most appropriate safety system for their application. Work with a trusted supplier who has demonstrated competency with a variety of safety sensors and protective devices, safe motion control, risk assessment, and machine validation for a comprehensive safety solution.
What is Fenceless Safety and Where is it Going
In this quick Q&A, SICK’s Director of Market Product Management, Steve Aamodt, walks us through the evolution of fenceless safety.
Q: What is fenceless safety?
A: Historically, work cells consisted of a machine with potential hazards safeguarded and surrounded by fencing. The idea is to be able to take that machine’s cell and open it up so you can increase productivity.
When there’s a fence around something, it’s hard to access—you can’t just walk right into the cell because there are work procedures to get in and out of the machine, it’s difficult to get material in and out, and so forth. The idea with fenceless safety is to remove those barriers and have full access to the machine, so it’s easy to get materials out, and you can reconfigure your manufacturing floor to quickly adapt to business conditions.
Q: Why is reconfigurability important?
A: What happens if you have multiple work cells configured to produce a specific part, and then you get an opportunity for new business where you need to unitize these cells? More than likely, you will need to tear down the fencing to reconfigure your production floor. If you implement fenceless safety, your production space is more open, and instead you’re looking at adjusting material flow or operational processes as opposed to physical machine changes. It’s easier to pivot.
On a simpler level, it also saves space. Typically, production cells are big and take up real estate. When you take down the fences and safeguard with a dynamic safety solution with safety scanners and SICK safety controllers, you can optimize your floor space. You get better efficiency out of the square footage you have. Ultimately, the goal is to have an open and free production floor.
Q: How do I know if it’s just as easy as taking out fences and putting in a safety scanner? What’s the process to apply one of these?
A: You need to understand the machine type, what tasks you are doing with this machine, and what hazards are associated with those tasks. Once your risk assessment is complete, you can design a safety concept to mitigate those machine hazards. Would a safety scanner work? Or possibly a safety scanner and a light curtain? Determine the safety concept that best fits your needs according to the risk.
Q: Where do you see the evolution of fenceless safety going for robotics?
A: Using sensor information and data, we can develop an understanding of where the people are in the facility and having them avoid potential hazards. Additionally, understanding the direction of movement of those people and intelligently moving the machines or working area away from where those people typically are. This removes the potential hazard and maintains efficiency.
Think of an airplane with a huge storm ahead. It automatically diverts around that storm in another direction to avoid the potential hazard. The same goes for robots and humans; intelligent safety sensors understand the relationship between human interaction and the machine to help avoid hazards or change the scenario for the risks.
Q: What’s the motivation behind this evolution?
A: Human safety and productivity. With increased demand, the time and production needs of producers require the process to be more efficient and intelligent, which helps them gain more productivity out of our systems.
Q: Do you see fenceless safety going the other way to more hard guarding? Why or why not?
A: Sometimes fencing is necessary. If you have debris flying from a machine, fencing could be a solution to help protect people and objects from this debris. Opto-electrical safety devices are not going to provide that protection. So, safeguarding is really a pragmatic approach. As safety sensor technology is evolving, becoming more intelligent and proving more data with the help of SICK, people are getting smarter in how they approach safety and keeping employees at the plant safe.