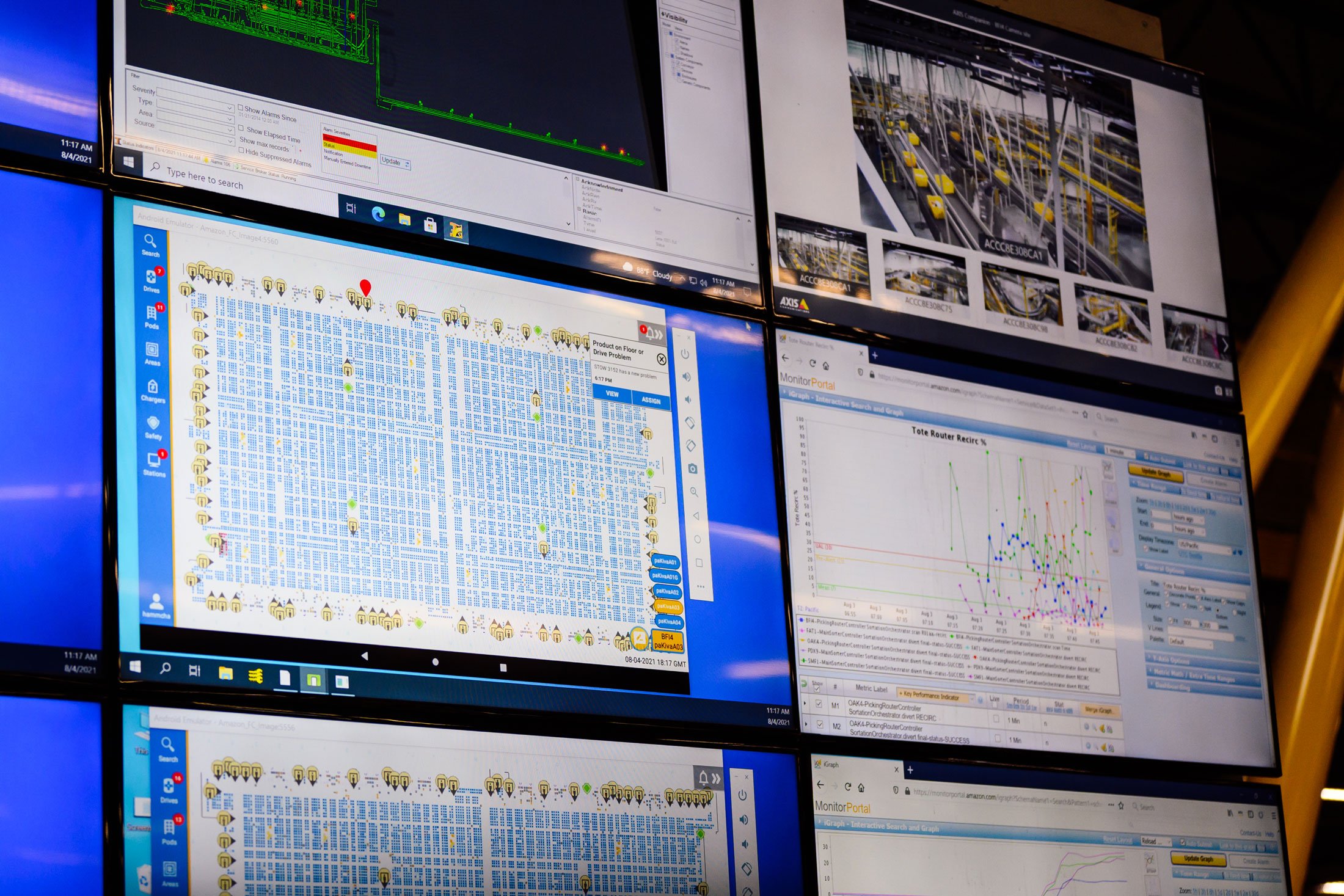
Warehouse Execution System
Introducing WORKFLOW™
〰️
Introducing WORKFLOW™ 〰️
WORKFLOW™ is not just a system; it’s your strategic partner in warehouse execution (WES). It flawlessly orchestrates and releases customer orders, granularly line by line, to your various warehouse resources—be it a fully automated ASRS such as AutoStore or traditional manual pick zones—such as case or piece-picking from racking to shelving, ensuring perfect orchestration every step of the way.
Smart AI, Smarter Decisions
At the heart of WORKFLOW™ is our cutting-edge AI machine-learning engine, which analyzes every customer's order with precision. Imagine a system that can simulate over 10 million ways to pick each line of an order and determine the optimal pick path, synching, and merging decisions—all in milliseconds. WORKFLOW™ guarantees that orders aren’t released until there’s assured inventory in each primary pick location, eliminating miss-ships and maximizing customer satisfaction.
Dynamic Response to Inventory Challenges
Should a primary pick location risk running low and not be replenished in time, WORKFLOW™ offers flexible solutions including ‘human-in-the-look’ options. It can alert a manager or make a real-time decision to either hold back the order or release it with specific line items back-ordered, automatically generating a follow-up order for the missing items. This proactive approach minimizes disruptions and keeps your operations running smoothly. Customers can be alerted and be sent messages informing them of their order status.
Human in the Loop: Integrating Human Insight
Our unique ‘Human in the Loop’ technology doesn’t just automate; it integrates human insight into AI-driven decision-making. This feature allows warehouse operators to choose when to automate and when to engage directly, ensuring that technological solutions complement human expertise rather than replace it.
Built for Today, Ready for Tomorrow
In today’s fast-paced supply chain environment, meeting rising customer demands while minimizing environmental impact is paramount. WORKFLOW™ is designed to absorb disruptions and foster resilience, ensuring your operations can adapt to both today’s needs and tomorrow's challenges.
WORKFLOW™ empowers businesses of all sizes to orchestrate their operations from end-to-end with efficiency and transparency. With features like multi-zone strategic order release and precise, second-by-second execution, WORKFLOW™ ensures that your warehouse operations are synchronized, visible, and optimized. Our platform provides real-time data visibility, enhanced scenario planning capabilities, and smarter decision-making for nearly perfect order execution.
Don’t Wait for the Next Disruption
Discover how WORKFLOW™, the leading modern warehouse execution solution, can transform your logistics operations. Contact us today to see how WORKFLOW™ can master every movement in your warehouse, from inbound to outbound, and turn your logistics operations into a competitive advantage.
Warehouse Automation’s WORKFLOW™—Mastering every workWORKFLOW™ movement, from inbound to outbound.
What is WES?
A warehouse execution system, or WES, is a software solution that can direct all of the processes that take place inside a distribution center. The WES works in real-time to organize, sequence and synchronize all warehouse resources: material handling equipment, devices, and employees. This reactive solution moves orders in a continuous flow. If a condition changes in one part of the process, the system will reprioritize work to expedite fulfillment.
WES vs. WMS vs. WCS
In the material handling industry, various software platforms are used to manage distribution operations. These platforms are commonly categorized as Warehouse Management Systems (WMS), Warehouse Execution Systems (WES), Warehouse Control Systems (WCS), and machine control systems. These terms have emerged to differentiate the key features and operational paradigms of these systems.
In addition to WMS, WES, and WCS, distribution centers often deploy other systems such as labor management systems, order management systems, material and resource planning systems, and transportation management systems. Together, these tools help manage different facets of an operation.
The Ideal Software System
In a perfect distribution environment, a single software platform would fulfill all operational requirements. However, such an all-encompassing platform does not yet exist. Instead, each system focuses on specific functions and operates within defined boundaries.
Key Differences: WMS, WES, and WCS
WMS: A Warehouse Management System is designed to create work plans. These plans can be developed well in advance, as timeliness is less critical to its operation. The WMS focuses on higher-level planning, such as inventory management, order tracking, and task assignments, rather than real-time execution.
WES: The Warehouse Execution System bridges the gap between the WMS and the resources—both human and mechanical—needed to execute work plans. Unlike a WMS, the WES provides real-time direction to ensure that people and equipment work together seamlessly to fulfill operational objectives.
WCS: A Warehouse Control System focuses on managing and directing material handling equipment. It operates in real time, issuing precise, time-sensitive commands to equipment. However, the WCS generally lacks broader decision-making capabilities and instead relies on higher-level systems, such as the WES or WMS, for operational direction.
Real-Time Decision Making
The most significant distinction between these systems lies in their approach to decision-making and timeliness:
The WMS creates plans without the need for real-time updates or immediate execution.
The WCS operates with real-time precision but functions within a limited scope, directing equipment based on external instructions.
The WES combines the strengths of both, making real-time decisions by assessing the status of all necessary resources—whether human or mechanical—at the moment of execution.
While some WMS platforms have improved their responsiveness, often referred to as “near real-time” operations, they still fall short of achieving the real-time operational control required for seamless integration across all work resources. Until WMS platforms fully close this gap, the distinction between WMS and WES will remain significant.
Adaptive. Scalable. Fast.
Warehouse fulfillment doesn’t have to be complex. FLOW® is a robust, customizable software solution designed to manage every process within your distribution center. Unlike traditional warehouse control systems, FLOW® goes beyond material handling equipment to integrate devices, people, and workflows. By synchronizing your workforce with equipment operations, FLOW® transforms fulfillment, much like Lean principles revolutionized manufacturing.
We provide a suite of modules, allowing FLOW® to be tailored precisely to your needs:
Dynamic Labor Balancing
Optimizes real-time labor distribution across multiple work zones.
Adjusts based on priorities and workload demands.
Synchronizes operations across all zones.
Minimizes inefficiencies by accounting for "zone transfer" penalties.
Sorting Machine Optimization
Implements real-time, optimized sortation decisions.
Boosts sortation capacity by 28%.
Reduces “problem orders” by 75%.
Lowers labor costs for processing and material handling.
Empowers workers to perform at their own capacity.
Next-Order Optimization
Releases orders in real time based on priority, shipment requirements, order age, picker locations, and inventory.
Ensures priority orders are processed immediately.
Identifies orders that cannot be picked under resource constraints.
Revolving Batch Picking
Eliminates unproductive wave transitions.
Promotes continuous resource utilization.
Balances operations, smoothing out productivity peaks and troughs.
Reporting & Management Tools
FLOW® VIEW includes over 150 pre-configured reports and management tools to keep pace with real-time distribution center activity. Its user-friendly interface also allows even beginners to generate custom reports in minutes.
Advanced Modules
FLOW® VIEW Mobility
Key features include:
Forecasting & variance analysis: Set production goals and track progress by shift.
Labor planning tools: Predict labor needs and allocate resources using historical production rates.
Performance alerts: Receive intuitive, early warnings on potential issues.
Remote control access: Turn equipment and workstations on/off from any device.
Browser-based access: Monitor operations from anywhere, anytime.
Responsive design: Works seamlessly across devices, orientations, and screen sizes.
Smart device RF integration: Replace costly RF devices with mobile-friendly alternatives.
FLOW® VIEW Analytics
This module expands on Mobility features, providing:
In-depth data visualization: Analyze operations with granular insights.
Drill-down capabilities: Uncover detailed information on key metrics.
Custom dashboards: Create tailored visualizations to optimize processes.
Cross-system reporting: Integrate and aggregate data from external databases.
Trend discovery: Track KPIs, spot trends, and make data-driven decisions.
FLOW® is the innovative solution to streamline operations, optimize resources, and elevate your distribution center to new levels of performance.
Software First
Warehouse Orchestration: The Next Great Supply Chain Breakthrough
Warehouse operations have become increasingly complex over the past decade. Labor shortages, enhanced customer demands, and an influx of data sources have all contributed to the fact that it's never been harder to run a warehouse efficiently.
Warehouse orchestration is a cutting-edge approach to managing the operational flow of modern warehouse environments. Orchestration involves synthesizing data from existing inputs — systems for warehouse management (WMS), labor management (LMS), transportation, production and inventory management — to create dynamic, optimized plans for the entire facility. It’s typically enabled by an orchestration platform, which provides a control layer over the top of existing software.
In short, warehouse orchestration helps get things out the door in the most optimal fashion. It simplifies labor forecasting and streamlines task execution to turn individual efforts into synchronized operations.
In recent years, distribution executives have expressed the need for greater visibility over their facilities, and better data to help them make informed decisions. But like many industries, warehouse operations can be slow to adopt new trends. According to a study by Zebra, 77% of warehouse decision-makers admit to being slow to implement new technology and devices, even if they recognize the need to modernize their operations.
Warehouse orchestration addresses the most common challenges of modern facilities. Going beyond a desire for analytics to tell managers more about the warehouse, it foundationally changes the way in which distribution facilities operate.
A handful of emerging trends have made warehousing more complex in recent years.
Growing complexity means that distribution operations are now non-linear, with every site juggling multiple workflows. Warehouse professionals with decades of experience might be able to coordinate around all these variables. But not every shift has a seasoned vet running the show.
An orchestration layer takes these shifting inputs, uses artificial intelligence to analyze them quickly, and produces a data-driven plan. It allows decision-makers to plan shipments more strategically, balance labor, and make life easier for shift managers and coordinators — even in the face of fluctuating demand.
Orchestration can increase efficiency, address data gaps and reinforce safety standards. Warehouse orchestration answers questions before they’re even asked. Teams don’t have to physically cross-reference dozens of reports or tools; orchestration platforms pull from inventory, activation plans, production and others variables to coordinate automatically.
It all comes back to the primary goal of many businesses: maximizing service levels. Less time strategizing means more time for pallet movements. The path to greater load readiness and higher fill rates is in motion.
Beyond the obvious productivity increases — which pay the bills —an orchestration system can help address data gaps and silos. Since orchestration coordinates data from various systems, it’s easy to identify when companies lack the requisite data inputs for optimal planning. And from a safety perspective, orchestration helps reduce congestion and create more efficient plans for staff.
A successful warehouse orchestration plan includes some baseline ingredients. Following are five elements to incorporate when building an effective warehouse orchestration strategy:
Warehouse complexity. An orchestration layer is likely only necessary for larger operations. If the warehouse has a linear process flow, only a few people in operation, or could easily be planned on a spreadsheet or whiteboard, a warehouse orchestration platform might not be a good fit.
Quality data. A certain level of data maturity is required for proper warehouse orchestration. The term “garbage in, garbage out” holds true for producing the most meaningful analytics. Required data points include inventory levels and locations, what needs to ship and when, production schedules when running a plant, and real-time visibility into transportation data.
Effective change management. Orchestration requires commitment. Rolling out AI systems in any network is complex. Decision-makers must lead by example and effectively communicate the status of changes to achieve buy-in. Companies with in-house champions can implement their orchestration strategy more effectively across multiple sites.
Well-defined SOPs. Building out great standard operating procedures is a prerequisite for orchestration. Baking the base-layer functions of day-to-day operations into orchestration software helps businesses achieve the vision that works best for their sites' unique needs.
Thoughtful training and communication. Help staff understand the value-add that orchestration brings to their jobs. Warehouse orchestration isn’t about replacing labor; it's designed to alleviate the annoying snags that arise in warehouses daily, so that staff can focus on more strategic work. Achieving buy-in means properly educating and training employees on the use and purpose of orchestration software.
Warehouse operations could use some modernization. Orchestration combines data and automation to maximize the value of existing staff and systems. The results include faster shipping times, less staff burnout, and more time for high-level decision-making. That's something everyone in the supply chain can appreciate.