Clever Robot Takes Unique Approach to Trailer Unloading
You may have encountered this video before: a robot stationed on a mobile base, ‘armed’ with a manipulator, deftly navigating into the rear of a trailer to suction up stacked boxes and efficiently transfer them onto a conveyor belt. Several robotics companies are engaged in this field, recognizing the ‘magic’ of automating trailer unloading workflows—currently marked by laborious, repetitive work that is less than ideal for human employees.
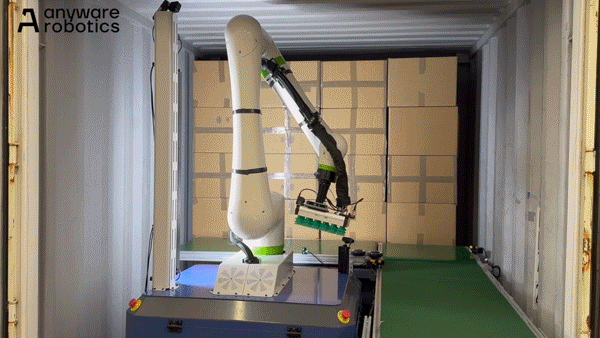
The design of Anywhere Robotics innovative solution, Pixmo, follows the familiar concept design of trailer unloading robots, albeit with innovative nuances. Pixmo offers a heavy-duty collaborative arm—a recent brainchild from Fanuc Robotics—ensuring compliance with ISO safety standards for human interaction. By outsourcing the heavy lifting to established suppliers and leveraging existing components, Anyware Robotics claims to streamline production, certification, and reliability testing, while focusing on innovation where it matters most.
Pixmo's mobility chassis base poses a unique challenge, as it must navigate short, steep ramps common in trailer loading bays—a problem conventional automated mobile robots (AMRs) struggle to solve. Thus, Anyware Robotics engineered a custom base to overcome this obstacle efficiently. Despite the tailored design, Pixmo remains cost-effective, with projections suggesting a third of the cost of competing solutions and a rapid return on investment within 24 months.
An innovative addition to Pixmo's standard solution is a conveyor system designed to complement its operations, reducing lifting efforts and minimizing box transfer distances. This enhancement not only boosts payload capacity but also significantly enhances throughput, with Pixmo capable of handling up to 1,000 boxes per hour.
Anyware Robotics plans to showcase their unique system at MODEX in March 2024, with a patent pending on the optional conveyor concept.
Introducing our New Packaging Automation Solutions
