Sky-High Warehouses: Chicago's Bold Multistory Pioneers
The 1.2 million-square-foot Chicago project began in August 2022 on speculation, or without leases signed in advance.
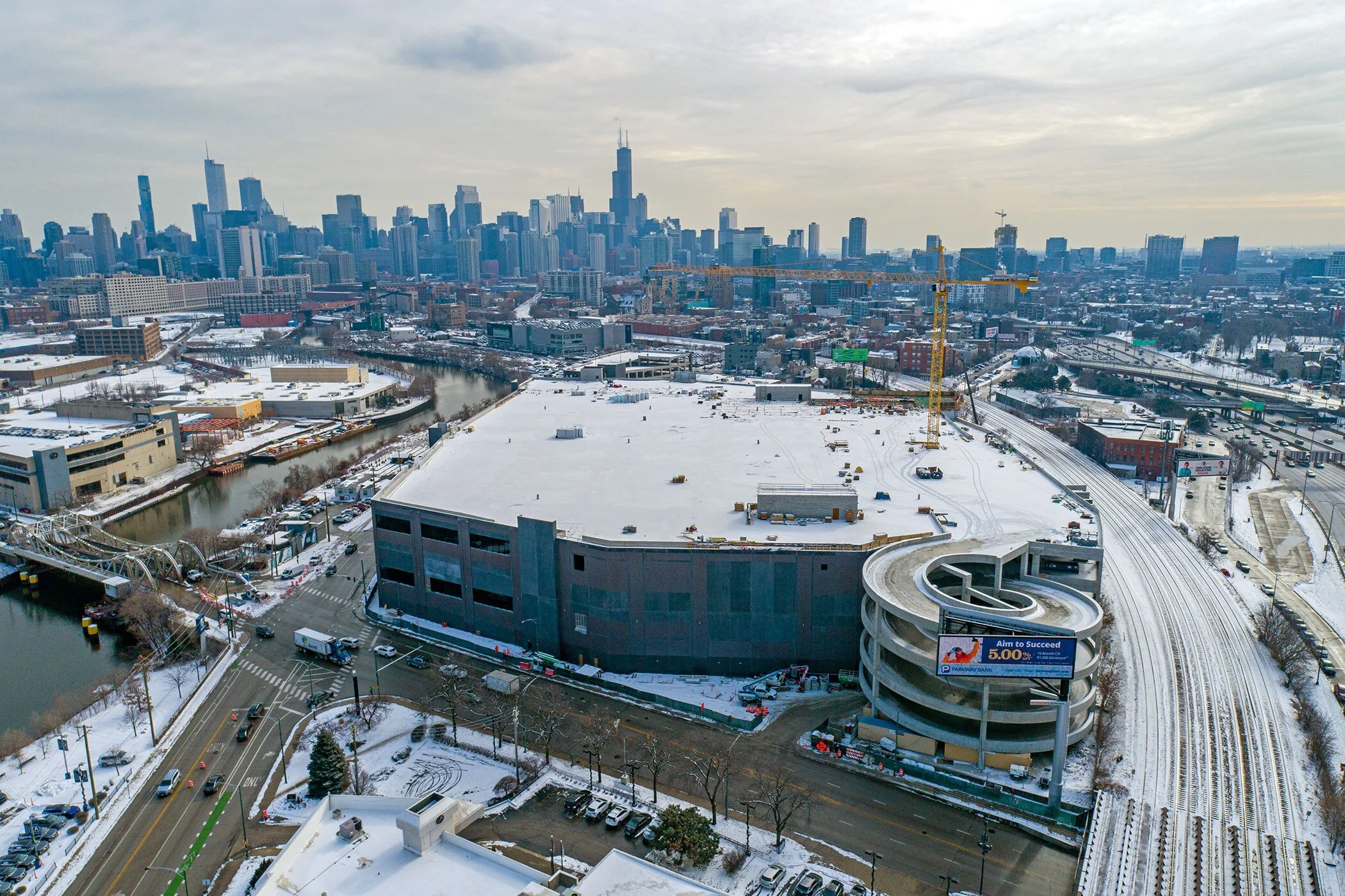
As Logistics Property Co. closed in on a deal to buy land near Chicago’s Goose Island in 2022, the firm had one major complaint: The well-located site wasn’t big enough to hold more than one big warehouse — or so they thought.
Turns out, it could contain more than one huge storage space, once the Chicago-based developer opted to essentially develop two distribution centers atop one another at 1237 W. Division St.
In the first project of its kind in the city, Logistics Property is in the late stages of constructing a modern, vertical warehouse supported by a series of ramps big enough to accommodate cars, delivery vans and trucks, and even full-sized semis — on more than one floor. The move throws down the architectural gauntlet to rival area developers, raising the bar on what can be done with warehouses.
Just months before the project is completed, and with no tenants signed yet, the fate of the vertical warehouse project is sure to be closely watched by rival developers, in Chicago and across the country. An expected completion in September comes as demand for U.S. industrial space remains far above typical levels, but below record levels seen earlier in the pandemic.
“It’s a collaborative market where you spend a lot of time with competitors,” said Aaron Martell, a founding partner and executive vice president at Logistics Property. “Everyone has a dog in the fight. Our dog is the biggest dog in the fight. I think people want to see it succeed because they want to see more of it.”
Multistory distribution centers are a phenomenon seen for decades in densely populated areas of Asia and Europe, but only in the past few years has it reached U.S. cities such as Seattle, New York and San Francisco.
The Chicago developer, which last year closed a $1.8 billion fund for projects throughout the country, decided to try its first vertical project on an 11.5-acre site it bought near a Kennedy Expressway interchange and the Chicago River. The firm said there are $2 billion in annual online purchases within a 5-mile radius of the site, an enticement for retail tenants to use such space to distribute orders onto trucks for delivery to doorsteps.
The 1.2 million-square-foot Chicago project began in August 2022 on speculation, or without leases signed in advance. Martell said interest from tenants has been strong, with e-commerce or other consumer products companies, grocers, package delivery companies and even movie production companies as potential tenants.
When completed, it will be the largest industrial space close to both the Loop business district and densely populated North Side neighborhoods.
Aside from the sheer size, the developer is betting that other attributes, including clear ceiling heights up to 36 feet and room for large vehicle fleets, will cause the facility — a pair of connected structures with two levels for product storage and five levels of parking connected to ramps — to stand out, particularly compared with older, smaller facilities on space-constrained Goose Island just across the river.
The Chicago project is nearing completion amid 6% overall vacancy nationally, far above the all-time low of 3.9% in mid-2022 but still well under the 20-year average of 7.3%, according to CoStar data.
Attabotics Inc., a Calgary-based robotics and automation startup, has filed for bankruptcy protection, according to multiple reports.
Peggy Johnson, CEO of Agility Robotics, discusses how humanoid robots like Digit are transforming logistics and manufacturing. She speaks with Bloomberg Businessweek's Brad Stone about the rapid advances in automation and the next era of robots in the workplace at Bloomberg Tech in San Francisco.
DHL Group has signed a strategic Memorandum of Understanding with Boston Dynamics, a global leader in advanced robotics.
In robotics, dexterity and perception go hand-in-hand, literally!
VenHub is a new concept in retailing – fully automated convenience stores run 24/7 by robots.
The Mini-Load ASRS is a storage retrieval machine designed to handle smaller loads such as cartons, totes, and trays.
Walmart is exploring automation with the grand opening of its flagship location in Canada.
NewCold’s Coaldale $222 million cold storage facility is expected to be operational by late June.
Enormous investments in factory equipment and artificial intelligence are giving China an edge in car manufacturing and other industries.
In just seven days, the 3D printed robotic assembly process for a new Walmart extension was completed in Huntsville, Alabama.
This would be the largest investment in warehouse distribution in Aldi’s network.
This disruption left key Myer-exclusive clothing brands trapped within the automated system, requiring manual intervention to resolve the ensuing stock-flow crisis.
See how automation is transforming CSV’s supply chain.
Equipped with cutting-edge automation, robotics, and machine learning technologies.
In the race of global economies, Canada stands at a crossroads.
TGH upgraded 10m customer orders to next-day delivery (NDD) in 2024, at no extra cost to customers.
The integration of RFID technology addresses a critical limitation: the ability to track inventory beyond line-of-sight.
The integration of RFID technology addresses a critical limitation: the ability to track inventory beyond line-of-sight.
The eGrocery market experienced significant growth in December 2024, reaching $9.6 billion.
The closures of US warehouses by Asos and Boohoo“mark a sobering reality check for their American ambitions.
The overarching trend is clear: technology and automation are becoming essential in modern warehouse and DC environments.
UBTech and Foxconn have signed a ‘comprehensive long-term partnership’ to deploy more robots in the iPhone maker’s factories.
The company was at pains to stress that it doesn’t represent any kind of retreat from America.
Cardinal Health will use a leading cloud-based warehouse management system that utilizes artificial intelligence.
Uber Eats is opening a new quick-service grocery delivery hub in Brooklyn with technology it says could “revolutionize” food shopping.
Interact Analysis's 2024 Mobile Robots Buyer Survey reveals growing but uneven mobile robot adoption across industries.
The vehicles are involved in nearly 100 deaths each year; companies say demand is growing for autonomous versions.
The robotics industry is buzzing with opportunities this year.
In the battle for e-commerce supremacy, there’s an uncomfortable truth retailers can no longer ignore.