Walmart Scales Automated Market Fulfillment Centers
MUSTANG, Okla. – Advanced robotic technology is being used to get online orders ready faster at a Walmart in Mustang, Oklahoma.
Their new market fulfillment center, or MFC, is the first fully operational one in the entire state of Oklahoma and is one of just a handful across the country.
“Layman’s terms, think of it as a six story vending machine,” said MFC store lead Chris Lone.
There are about 90 robots in the six story structure within the 35,000 sq. ft. facility connected to Mustang’s Walmart Supercenter off SH-152. They fulfill about 550 online orders per day with a main goal of more orders in less time.
“I feel like we’ve been in such a great job and be able to enhance the customer experience by increasing the capacity,” said store manager Scott Langston.
Here’s how it works. A customer orders online and the system determines if it’s available in the MFC. If it is, employees pick it out using their technology.
“We will pick ambient, chilled, frozen,” Lone said. “We do all three chambers here.”
From there, the robots inside the structure go and get it. Lone said a majority of the items in the MFC are usually the one’s purchased the most.
“The idea is 10 to 12 minutes total time to be able to get it picked, get it staged, get it sent out based on from the time they order,” Lone said.
After it’s all sorted out, employees take it straight to the customers car. Lone said it saves 5 to 8 minutes of time. He added it can add up to with customers normally sifting through items and traffic in store. Other employees like Langston that deal with the technology said it makes their lives easier too.
“I think we’ve increased the associate experience as well by reducing friction and making their job much easier,” he said.
The next fully operational MFC in Oklahoma is set to be in Broken Arrow later this month.
From Ground-Breaking to Breaking Ground: Walmart Begins to Scale Market Fulfillment Centers
A market fulfillment center (MFC) is a compact, modular warehouse built within, or added to, a store. In addition to fresh and frozen items, MFCs can store thousands of the items we know customers want most, from consumables to electronics.
Instead of an associate walking the store to fulfill an order from store shelves, automated bots retrieve the items from within the fulfillment center. The items are then brought to a picking workstation, where the order can be assembled with speed.
While the system retrieves the order for assembly, a personal shopper handpicks fresh items like produce, meat and seafood, and large general merchandise from the sales floor.
Once the order is collected, the system stores it until it’s ready for pickup. This whole process can take just a few minutes from the time the order is placed to the time it’s ready for a customer or delivery driver to collect.
Walmart began piloting its first market fulfillment center in Salem, New Hampshire, in late 2019. The technology has shown impressive results such as:
More availability: Able to pick more orders and do it quicker, creating more availability for customers.
Faster fulfillment: The system’s speed can allow orders to be picked up or delivered within the hour.
Greater efficiency: One market fulfillment center can fulfill orders for many stores, which means its benefits can be felt by customers in stores nearby.
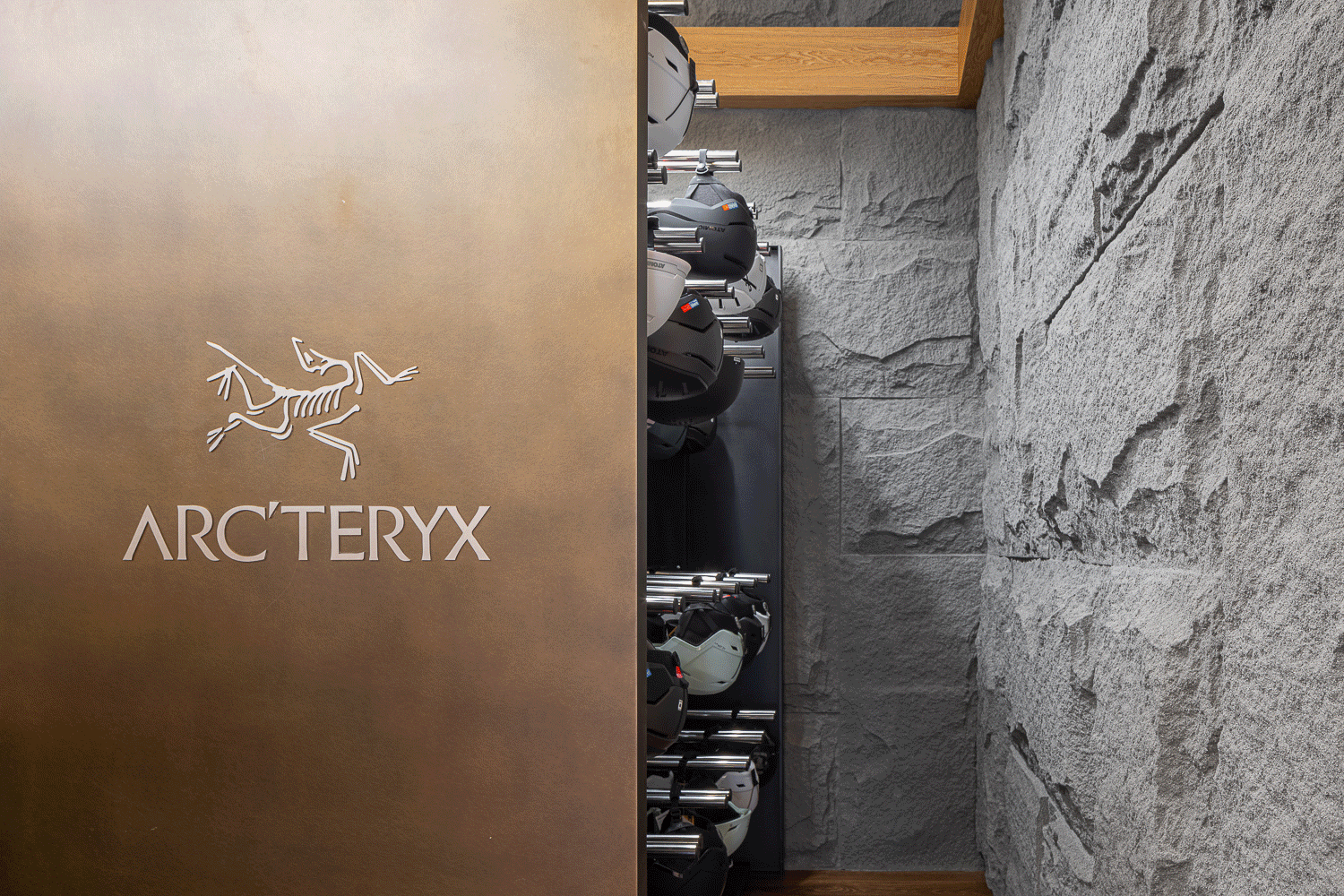